集团动态 News Information
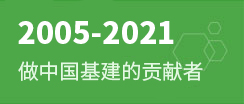
聚羧酸减水剂聚醚大单体工艺技术简析
摘要:
聚羧酸减水剂是一种新型环保的减水剂,是国内外减水剂研究的热点。当前,聚羧酸减水剂生产工艺所采用的聚醚大单体主要是MPEG大单体、APEG大单体、TPEG大单体、HPEG大单体。本文主要介绍聚羧酸减水剂聚醚大单体生产的种类并介绍三种聚醚大单体的生产工艺过程及其控制因素。
0 引言
混凝土作为当今世界主要的建筑材料,其性能指标很大程度上受到减水剂的影响。聚羧酸减水剂作为当今使用效果最好的新一代减水剂,其大规模用于铁路、轨道交通以及其他建筑用混凝土中。近几年来,作为聚羧酸减水剂生产所必须采用的原料载体,聚羧酸减水剂聚醚大单体在我国乃至世界范围内研究发展很快,成为了减水剂研究和应用中的主流,研究方向主要体现在合成大单体的结构和合成工艺条件方面。
1 聚醚大单体种类
随着经济社会的发展,国内聚羧酸减水剂合成用聚醚大单体已从最初的MPEG(聚乙二醇单甲醚)发展到现在的APEG(烯丙基聚氧乙烯醚)、TPEG(异戊烯基聚氧乙烯醚)和HPEG(甲基烯丙基聚氧乙烯醚),其中TPEG和HPEG大单体已占据国内最大的市场比例。
MPEG合成减水剂,一般包含聚合、酯化2个环节,且由于MPEG不能完全酯化,残留在产品中的MPEG会极大的影响减水剂的应用性能,造成产品质量不稳定。
APEG合成减水剂,只需将其与起始剂单体溶液聚合便可制备。但APEG聚合活性较差,与MPEG单体类似残留量较大,得到的减水剂性能不稳定,目前产量逐年降低。
TPEG和HPEG合成减水剂,已成为国内市场上的主流品种,其聚合活性好,同时具有很好的减水率,工艺技术已经非常成熟。
2 聚醚大单体生产工艺
聚醚大单体生产工艺历经近百年的发展,已成为一种较为成熟的工艺技术。该工艺是指以环氧乙烷(EO)为原料,与各类起始剂(比如分子内含有活泼氢的乙二醇、脂肪醇等)在催化剂作用下发生加成聚合反应,生产各种规格的聚醚大单体产品。这类生产工艺的特点主要包括:①反应过程包括:氮气置换、进料、预反应、反应、熟化、脱挥、排料、洗釜(可选择)等步骤;
②反应是强放热反应(反应热约为2140kJ/kgEO);
③反应为间歇反应,产物粘度大,易堵;
④反应原料含环氧乙烷(EO)气体(易燃易爆且高毒),一旦泄露极易发生火灾和爆炸造成重大安全事故。
基于该生产工艺的特点,其生产技术也经过了不断的改进,先后经历了传统搅拌工艺、喷雾式生产工艺、环路喷射式生产工艺。
2.1 传统搅拌反应器
在传统搅拌反应器中,液相EO通入罐底分布器鼓泡,在搅拌器作用下与起始剂反应,反应热由冷却夹套和内部的冷却盘管移去。
传统搅拌反应器存在较为明显的缺点:
①未反应的液相环氧乙烷,有在罐内积累的可能,一旦开始反应会迅猛放热,导致温度和压力骤升引起设备爆炸;
②反应器顶部积聚了大量未反应气相环氧乙烷,与搅拌器的旋转部分接触,有可能会自聚或旋转部件产生静电或火花而带来危险;
③由于物料之间的接触是在环氧乙烷进入罐内汽化鼓泡时进行的,反应物料和催化剂之间的接触不均匀,导致副反应物的生成;
④反应速度低,物料在高温下停留时间较长,产品色泽加深。
因此,国内新建项目,一般已不采用传统搅拌式反应器。
2.2 气液接触式喷雾反应器
意大利Press公司开发的气液接触反应器,该工艺采用雾化的物料(液相)分散到EO气相中。
该反应器的特点在于:
①反应器中接触EO气相没有旋转部件,防止静电形成,且循环物料中EO含量低,操作十分安全。
②环物料形成雾状与环氧乙烷气相接触,反应速度快,每立方米反应器的E0消耗速率在1200kg/h,同时生成的副反应少,产品质量高。
③在含惰性气体的气相中仍有较高的反应速度,环氧乙烷与惰性气体之间没有分层的可能性,操作处于爆炸极限之外。
④产品的分子量分布范围小,利于质量控制。
⑤其工艺技术和设备已经全部国产化。
Press工艺有三代反应装置,根据原料和产品性质不同而选择。第一代反应装置,加催化剂脱水、主反应、中和反应及循环产品贮存均在一个反应器内完成,产量低、设备利用率低,适合生产规模较小的企业;第二代反应装置,将预反应(加催化剂)、主反应、中和反应在三个系统内完成,主反应装置由反应器、反应贮罐和循环物料换热器组成,设备利用率高,适用于规模较大企业;第三代反应装置,适用于生产较高分子量的产品,在装置系统中增加了小循环换热器。
这三代反应器的共同点是喷雾型气液接触反应,主要不同点在于链增长比。第一代和第二代反应器使原料与乙氧基化产物的体积增长比分别为1:7和1:12。第三代反应器的体积增长比可达1:20~1:40。
目前,国内新建的醇醚装置,大多采用仿Press公司的技术。
2.3 环路反应器
瑞士布士(BUSS)公司开发了环路反应器,环路反应器是利用文丘里原理,将液体物料从反应器底部抽出,通过外置换热器后进入喷管,在喷管局部形成负压,将EO气体吸入,在喉管处气液分散十分均匀而进行加成反应,此时物料为连续相,而环氧乙烷为分散相。同样,环路反应器适用于规模较大的生产企业。该装置可与Press公司的工艺技术媲美,其反应速率甚至高于喷雾接触式反应器,同样可以得到高质量的产品。
其工艺主要特点为:
① 反应设备少,工艺流程简单,布置方便;
② ②反应速度较快,适合生产黏度较大的品种;
③ ③不需进行脱气处理,产品中游离EO含量即可达到1mg/L以下;
④ ④反应安全性高,生产过程在氮气保护下,可确保反应器内可燃气体在安全范围内;
⑤ ⑤循环死角少,更换品种时洗釜简单,甚至可直接用氮气吹净即可。
⑥ ⑥可采用粉末催化剂,省去了催化剂配置工序。
3 聚醚大单体生产工艺主要控制点
3.1 催化剂的选择
生产聚醚大单体产品时,催化剂在聚合过程中具有决定性的作用,它不断极大地影响产品收率、相对分子质量分布,还会对最终的减水剂合成产生影响。现阶段催化剂大多采用KOH、NaOH、NaH或Na等几种催化剂。除固体NaH或Na作为催化可直接使用外,KOH、NaOH溶液一般现场配置。综合多年生产实践,使用KOH时催化效率最高,能有效的缩短反应时间。但无论使用何种催化剂,聚合反应随着催化剂用量的增大,反应时间都会缩短,但当催化剂用量达到总进料量的0.5%时,反应时间降低的幅度会越来越小。
3.2 反应温度的选择
反应温度的高低会直接影响反应速度。反应温度高,聚合速度快,反之聚合速度慢,但反应温度过高,会导致副反应产物的增多。在恒定催化剂用量的前提下,反应温度一般控制在120~125℃时为最佳。当温度区间在90℃~120℃之间时,反应进行得很慢,极大的延长了反应时间,也间接提升了生产成本,并且由于大量原料未参与反应,温度升高时容易暴聚,发生危险。当温度大于125℃时,反应速率显著加快,但副产物含量也明显增多,并且双键极易被破坏,影响产品性能。
3.3 其它反应条件
未参与反应的游离EO、原料带入的水汽及热分解产生的微量轻组份,依靠真空脱挥进入尾气碱洗塔洗涤处理,所以脱挥真空度会很大程度影响产品性能,现阶段一般采用蒸汽喷射加真空泵两级抽吸,以期达到尽可能大的真空度。
产品pH值主要依靠中和剂调节,现阶段主要采用弱酸醋酸参与实现,理想pH值控制在7~8之间为宜。
4 结语
随着国民经济的高速发展,特别是在2013年习近平总书记提出“一带一路”战略之后,高性能混凝土的需求将持续扩大,这必将极大的刺激聚羧酸减水剂的需求量,作为减水剂合成必须的聚醚大单体原料,其发展前景无疑将更加广阔。