集团动态 News Information
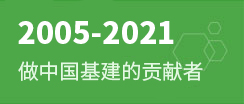
对半个世纪水泥质量发展道路的反思(三):水泥质量发展方向的修正
在回顾世界水泥质量发展道路的基础上,已经分析了水泥质量变迁与混凝土耐久性劣化的关系。库马尔·梅塔和理查德·W·伯罗斯[3]总结了近百年美国混凝土发展道路,他们提出与混凝土耐久性有关的水泥方面的问题,包括:①水泥用量增加了;②水泥强度特别是早期强度高了;③水泥C3S多了;④水泥比表面积增加了。
国内学者也有类似的意见。但对于如何解决这些问题,水泥和混凝土两方面的意见很难统一。水泥方面似乎被禁锢于一种传统的思维定势之中,认为一百多年以来已经建立并不断完善的通用硅酸盐水泥技术指标体系,其框架是无需置疑的,只需进行一些细节上的小的修补。
混凝土方面又较少考虑他们的意见对于水泥行业需要付出的一系列巨大代价,这些代价包括经济的、能源的和环境的。本文试图根据混凝土耐久性的需要,探讨对通用硅酸盐水泥技术指标体系框架的修改。在满足混凝土耐久性需要的同时,水泥行业如何以最小的经济、能源和环境代价,实现对水泥质量发展方向的修正。
1水泥质量发展方向存在的问题
最近的十余年间,来自于混凝土方面对水泥质量的批评已经很多,提出了许多具体存在的问题。但很少有人指出,半个多世纪,甚至可以将时间追溯的更早一些,水泥质量的发展道路与混凝土耐久性的要求是背道而驰的。真正认识水泥质量发展方向的错误,并进行修正,才能保证混凝土结构的耐久性。
总结目前水泥质量存在的主要问题如下:
1)水泥强度特别是早期强度偏高;
2)水泥细度细;
3)熟料C3A含量偏高;
4)熟料C3S含量偏高;
5)水泥的碱含量偏高;
6)夏季出厂水泥温度偏高。
上述问题导致:
1)水泥早期(水化后数分钟至3d)化学减缩增加;
2)水泥早期水化热增加;
3)水泥在数年及更长时间持续的强度增长能力减弱,甚至消失;
4)水泥开裂敏感性增加。
除前述水泥质量存在的主要问题之外,还存在以下的一般性问题:
1)仅以水泥的凝结时间、强度作为确定石膏掺量的依据。实际上水泥中石膏的掺量和形态与流变性能、开裂敏感性均密切相关。
2)水泥磨尾仓使用段做研磨体,导致水泥颗粒形貌变差。
3)使用料床粉磨作为水泥终粉磨,导致水泥颗粒形貌变差。
4)水泥标准对水泥与减水剂相容性未作规定,实际水泥于此参差不齐。
5)水泥标准没有全面的水泥质量匀质性指标,水泥质量波动大,偶尔发生用户非预期的、不可知的巨大变化。
将上述问题归纳总结,以混凝土耐久性破坏进行溯源,水泥质量存在的本质性(核心)问题有两项:1)水泥早期水化速率过快;
2)水泥碱含量偏高(主要指三北地区而言)。
其余问题均可视为是这两个本质问题的现象或原因。碱含量偏高固然是水泥早期水化速率、化学收缩过大的原因,但除此之外,碱会劣化水化产物形貌。或许有人主张将化学减缩加大、水化热增加也列入导致混凝土性能变差的本质原因。化学减缩增加实际上是因为水泥早期水化速率加快,使水化产生的化学减缩在早期的测量结果增加了,并非真正的减缩增加。
真正能够减小混凝土化学减缩的措施,只有降低水泥用量。水化热的情况也与化学减缩近似,只是化学减缩在混凝土初凝之前是少害或无害的,水泥浆体硬化之后才会产生危害。水化热在水泥浆体硬化之前和之后都是有害的,只有在混凝土达到最高内部温升之后,水化热的危害才会变小以致消失。因此,早期化学减缩、早期水化热增加也可以视为水泥早期水化速率高的结果。
水泥行业普遍存在的一些不利于混凝土性能,特别是有害于混凝土耐久性的做法:
1)水泥强度等级越高(熟料含量越高),细度越细;
2)通过提高熟料C3A含量提高水泥早期强度或提高窑的台时产量;
3)要求熟料鲍格公式计算的C3S含量大于一个很高的数值,例如60%;
4)水泥磨尾仓使用段做研磨体;
5)使用料床粉磨作为水泥终粉磨;
6)在水泥粉磨过程中加入以碱金属盐为主要成分的激发剂。
2混凝土若干技术要求辨析
半个多世纪水泥质量的变迁,碱含量的提高是由于水泥企业为了降低能耗、提高窑单位容积产量,主动采用窑外分解窑技术造成的。除此之外,C3S含量增加、早期强度提高以及细度变细都不是水泥企业的主动行为。水泥质量向错误方向的演变,是在水泥使用者不断给水泥行业以误导造成的。这种误导有一些是技术性因素,也有一些是非技术性因素。例如水泥早期强度的不断提高,是由于混凝土早期强度的要求,而混凝土早期强度提高又是业主、施工方的要求。在与建筑物有关的多方复杂关系中,总能看到利益、政绩驱动的因素。今天,当水泥企业考虑修正水泥质量发展方向的时候,应该特别注意不能因为缺乏沟通与研究,再次受到水泥使用方的误导。
毋庸置疑,半个多世纪以来混凝土耐久性劣化,很大一部分原因源于水泥强度特别是早期强度提高,细度变细。但如果混凝土行业要求水泥行业一定要降低水泥早期强度和细度,将可能再一次对水泥行业造成误导。事实上导致混凝土耐久性劣化的是水泥的早期水化速率快,熟料的C3A、C3S含量高,水泥中熟料细颗粒多。
2.1水泥强度
理查德·W·伯罗斯在分析美国半个多世纪以来混凝土耐久性变差的原因时,特别强调水泥早期强度不断提高的危害[6]。但降低水泥早期强度对于混凝土耐久性是充分条件而非必要条件。换言之,降低水泥早期强度对混凝土耐久性有利,但危害混凝土耐久性的本质,不是水泥的早期强度高,而是水泥的早期水化速率快。如果在提高水泥早期强度的同时,不加快水泥的早期水化速率,则对混凝土耐久性没有明显危害。
水泥早期水化速率高的原因包括:①熟料早期水化速率(强度)高;②水泥中含有较多的熟料细粉(<3μm);③水泥中石膏的形态和数量没有得到正确的优化;④碱含量高。将上述关系归纳如图1所示。
图1水泥早期强度影响因素分析
半个世纪以来,我们几乎将水泥质量与水泥强度等同,同时又将水泥活性与水泥强度等同。认为提高水泥活性是提高水泥强度的唯一途径。而忽视了水泥强度的物理作用,忽视了通过优化水泥的粒度分布,提高水泥水化前的堆积密度,可以在显著提高水泥强度的同时降低水化速率这一重要事实。
对于强度认识的误区包括:
1)首先是水泥、混凝土的唯强度论:强度第一,甚至强度唯一。这一错误的观念从混凝土传递到水泥行业,多年来已经深入人心,许多人认为不容置疑。
2)其次是水泥强度的唯化学论:把活性、化学反应能力与强度等同,认为强度的唯一来源是水泥(或混合材料)的化学反应能力。一个连带的误区是认为水泥高强必然高水化热。
3)将按照标准方法检验(固定水灰比)的只具有相对意义的强度数值绝对化。事实上,强度是水灰比、龄期的函数。
唯强度论的出发点也许不错,但结果却令人沮丧。有人为了避免混凝土路面的损坏,将混凝土路面板的28d抗折强度提高到5MPa。随着混凝土强度增加,其脆性也同时提高。
对因冲击荷载而疲劳断裂的水泥混凝土路面,高脆性将使其更加无法耐久。高强的同时必然是高脆性的、易开裂的混凝土,很难承受冲击载荷。地震时的建筑物、混凝土路面、受到轮船撞击的桥墩都是承受冲击载荷。
1957建成的武汉长江大桥,半个多世纪以来历经了近80次撞击,无结构性损坏。最严重的一次是一艘万吨级油轮正面撞上了武汉长江大桥的7号桥墩。武汉长江大桥桥墩使用的是抗压强度15~20MPa的混凝土。1988年建成的广东九江大桥,2007年被一艘2000吨级的运砂船撞击,发生160m垮塌。近年来桥梁混凝土的抗压强度已经提高30~50MPa,但被船撞垮桥梁的事故频现。
唯化学论是又一个错误的思维定势。水泥强度的唯化学论忽视了水泥石强度的本质。20世纪60年代,T.C.Powers基于对水泥石结构的假设及大量试验结果,提出了反映水泥石强度与其孔隙率关系的胶空比公式:R=α0·Xn
式中:
R——水泥石强度;
α0——水泥凝胶的固有强度,即凝胶体在孔隙率为0时的强度;
n——试验常数,约为2.5~3;
X——胶空比,即水泥凝胶在水泥石中的填充程度,大小为凝胶体积与凝胶体积加毛细孔体积及气孔体积之和的比值,主要与水灰比和水化程度有关。
水泥石孔隙率大小主要取决于水灰比。从水泥的水化硬化过程而言,决定水泥强度的因素可以分为化学作用和物理作用两个方面。在水泥中含有较多熟料及高活性的混合材料,或熟料、混合材料的活性较高,都可以产生较多的水化产物,从而减小孔隙率,提高强度。
同时,如果提高水化前水泥颗粒的堆积密度,可以降低用水量,同样可以降低水泥石的孔隙率,提高强度。利用物理作用提高水泥强度,特别是提高早期强度,可以使用较少的熟料,在大幅度提高强度的同时,降低水化热。采用分别粉磨工艺,按照各自不同的要求分别控制熟料、混合材料的粒度分布,配制水泥时对粒度分布进行设计与控制,可以生产含有60%的熟料的水泥,3d抗压强度高于熟料6MPa,28d抗压强度高于熟料14MPa。同时水化热降低。
日本水泥的粉磨工艺处于世界领先水平,分别粉磨技术在日本50年前就已经开始应用,40年前已经全部淘汰了混合粉磨工艺。笔者1999年在日本水泥厂看到的关于水泥强度的一个普遍现象是,与熟料强度比较,掺有15%混合材料的水泥,3d抗压强度高于熟料5MPa,28d抗压强度高于熟料10MPa。掺有50%混合材料的水泥,3d抗压强度略低于熟料,28d抗压强度略高于熟料。这已经足够满足配制C60混凝土的需要。
不能将化学反应能力误认为是强度的本质。强度的本质是孔隙率。所有能够降低孔隙率的措施都可以提高强度。水泥的粒度分布经过设计之后,强度可以提高到令我们吃惊的程度。即使是石灰石这样的惰性物质,如果足够细,也会有很高的强度贡献,在水泥中等量替代熟料后,甚至会超过替代前的水泥强度。转变思维模式,摒弃唯化学论,我们就可以生产出具有很高强度,同时水化热很低的水泥。
2.2水泥细度
当希望与水泥性能建立联系时,水泥细度的含义不够明确,因为与水泥物理性能相关的是水泥粒度分布,筛余或比表面积只能作为水泥厂粉磨工艺一个控制指标。在混凝土行业很多人将细度与筛余等同。
与水泥早期强度类似,粗水泥也只是混凝土耐久性的充分条件而非必要条件。混凝土要求水泥不能过细实际上想要表达的是:水泥过细会加快早期水化速率、提高早期水化热、增加早期收缩、提高减水剂掺量、增加坍落度损失。
但事实上造成上述现象的主要是过细的熟料颗粒,混合材料(于混凝土则为掺和料)过细基本上不会导致上述问题。水泥中不同组分(熟料、石膏、混合材料)的水化行为不同,在水泥石微结构中的作用不同,对水泥性能的影响不同,粒度分布的要求也不同。
在探讨水泥最佳粒度分布时必须分别考虑[9]。即分别研究熟料粒度分布、混合材料粒度分布和水泥粒度分布的要求。水泥中熟料的粒度分布要求是在保证较低细颗粒含量的前提下,尽量提高水化程度,熟料粒度分布应符合最佳性能RRSB方程。混合材料粒度分布要求是,与熟料配合后提高水泥颗粒的堆积密度使得熟料+混合材料组成的水泥的粒度分布符合Fuller曲线。
仅从水泥细度角度而言,符合现代混凝土要求的水泥应:①单方混凝土中尽量低的熟料含量;②早期(数分钟至3d)尽量低的水化速率;③28d之内足够的水化程度,且保持5~10年持续提供水化产物的能力;④粉体颗粒具有较高的堆积密度。目前我国广泛应用的采用混合粉磨工艺的水泥,不符合上述要求。为满足上述要求,熟料的细粉(<3μm颗粒)要有一个较低的限量,笔者建议一般性的标准 <10%,严格标准<8%,同时混合材料更多地含有细粉。这需要采用分别粉磨工艺。
2.3需水量
在水泥和混凝土行业都有“需水量”这一简称,但其含义不同。在混凝土行业需水量指单方混凝土用水量,在水泥行业需水量指水泥标准稠度用水量。
水泥标准稠度用水量包括4个部分:①固体颗粒表面的吸附水(包括颗粒之间空隙的水);②水泥初始水化消耗的水;③稀释水泥初始水化产物的水;④火山灰质等具有开口孔和内比表面积的材料吸附到材料内部的水。混凝土用水量的组成与水泥标准稠度用水量大致相同,多出了砂石表面吸附水,但各部分的比例不同。
混凝土单方用水量并不是水泥标准稠度用水量的单值函数,其影响因素包括:①水泥的标准稠度用水量;②水泥与减水剂相容性;③减水剂的质量和用量;④粉煤灰的含碳量;⑤砂石材料的含泥量;⑥混凝土所有胶凝材料的粒度分布。对于今天已经普遍使用减水剂的流态混凝土,水泥标准稠度用水量与单方混凝土用水量不能简单对应的原因还在于,检验水泥标准稠度用水量时没有减水剂的存在,而拌和混凝土时使用了减水剂。
使用减水剂后固体颗粒(主要是粉体颗粒)表面的吸附水(包括填充颗粒之间空隙的水)明显减少。有一个能够说明问题的例证:向水泥中掺入20%的很细的矿渣粉,例如比表面积600m2/kg,水泥的标准稠度用水量是增加的。用这种水泥拌和的混凝土用水量却是减少的。对这一现象混凝土行业称为矿物减水效应。
3对水泥质量发展方向的修正
前文[1-2]及本文已经尽量充分讨论了当今混凝土耐久性变差与水泥质量的密切关系。今后我们能否沿着过去几十年水泥质量的方向继续前行?答案显然是否定的,混凝土耐久性不允许。能否转身向后,重新回到几十年前?答案同样也是否定的,巨大能源和环境的压力使然。我们应该寻找一条更好的途径,以较小的能源、资源、环境和经济代价达到既定目标——生产可以使混凝土耐久的水泥。以下笔者试图对此进行探讨。
讨论水泥质量发展方向的修正,或水泥质量的改善,是基于这样的认识:①半个世纪以来,中国与世界其他发达国家一样,水泥质量是在沿着一条错误的方向发展;②通用水泥标准体系的框架必须进行根本性的修改。在研讨修正水泥质量发展方向的时候笔者特别强调范式转换。
3.1难以改变的对混凝土耐久性不利影响因素
主要是熟料C3S活性、碱含量,尽管它们影响显著,但难以改变。
3.1.1 熟料C3S活性
水泥早期水化速率高的原因已如图1所示。其中熟料C3S数量和活性的增加是半个多世纪以来水泥质量方面最大的变化。20世纪70年代窑外分解窑和与之配套的高效篦冷机开始应用,显著提高了熟料的煅烧强度,熟料高C3S含量成为可能。不仅熟料中鲍格公式法计算的C3S含量可以高达60%以上,而且,窑外分解窑普遍采用快烧急冷的工艺方式,一方面使得熟料中实际存在的C3S可以比鲍格公式计算值高8%~10%(绝对值);另一方面,熟料中的硅酸盐矿物晶格缺陷显著增加,使得熟料水化反应速率增加。这些都使熟料早期水化速率显著加快。由于我国一直采用混合粉磨工艺,水泥中熟料细粉的含量随着水泥细度变细而增加。这又使得水泥早期水化速率增加。熟料C3S数量可以通过降低KH调整,但其活性却很难降低,或者说降低C3S活性需要付出很高经济、能源和环境代价。
3.1.2 熟料碱含量
熟料碱含量是伴随预热器窑和窑外分解窑的普及和窑系统粉尘排放量减少而提高的,原因在于预热器窑和窑外分解窑在窑内高温区进入气相的碱,无法像其他窑型那样在窑外冷凝到粉尘表面排除到窑外,所有原燃材料带入的碱几乎全部留在熟料中。除非在水泥厂附近找到低碱的替代原料,否则能有效降低熟料碱含量的措施只有旁路放风,但这会显著增加热耗。对于新建水泥厂可以慎重选择厂址,避免使用高碱原料。
3.2对水泥质量发展方向的修正
既然已经明确水泥存在的本质性问题是早期水化速率快、碱含量高,那么对水泥质量修正的方向也就明确了。降低碱含量的困难已如前述。如果不能以较低的代价降低碱含量,要解决的核心问题就是降低水泥早期水化速率。技术路线如图2所示。粗线部分为重点内容。
图2 降低水泥早期水化速率技术路线
对于图2给出的技术路线,可以概括表述为:使用低C3A、C3S的熟料,采用分别粉磨工艺,生产早期水化速率低,而强度并不太低的水泥。
3.3优质水泥的基本特征
早年笔者曾经提出若干从保证混凝土性能特别是混凝土耐久性考虑的,优质水泥的基本特征:
1)单方混凝土的熟料用量较少;
2)较低的早期水化速率和水化热;
3)与高效减水剂具有良好的相容性;
4)全面的水泥质量匀质性指标;
5)合理的早期、后期强度和至少保持10年内持续的强度增长;
6)粒度分布合理,颗粒球形指数高,堆积密度高;
7)较小的体积收缩;
8)适宜的碱含量;
9)夏季较低的出厂水泥温度。
3.4提高混凝土耐久性水泥生产的技术措施
为提高混凝土耐久性,水泥生产可以采取的主要技术措施包括:
1)改变熟料矿物组成:C3A<5%,C3S<50%。
2)尽量降低熟料中的碱含量,同时控制硫碱比不低于0.8。
3)水泥粉磨采用分别粉磨。熟料+石膏的终粉磨采用球磨机+高效选粉机(选粉效率90%以上),以期得到形貌良好、粒度分布集中的熟料粉。熟料粉RRSB均匀性系数达到1.35以上。
4)混合材料粉磨优先选择立磨,并粉磨至多种细度分别储存,惰性材料(如石灰石)最细。
5)对水泥的粒度分布进行设计、控制,使得熟料粉+多种混合材料粉组成的水泥的粒度分布符合Fuller曲线。
6)以水泥的早期水化速率、流变性能和开裂敏感性作为确定水泥中石膏种类、掺量的优先依据。
7)出磨水泥经过至少3d库存后出厂。
8)夏季降低出厂水泥温度至80℃以下。
3.5 对通用硅酸盐水泥标准进行根本性修订
尽管我们时常以水泥标准是最低质量要求为理由,拒绝对水泥标准的修改,但水泥标准对水泥质量巨大的引导作用使得我们欲改变水泥质量,必须先改变水泥标准。对此笔者建议:
1) 建立低水灰比(在0.38~0.40之间选取固定值)强度检验方法,废止现行ISO强度检验方法(出口水泥可以保留);
2)增加熟料鲍格公式计算C3A、C3S的上限指标;
3)增加熟料硫碱比下限指标;
4)增加水泥早期水化速率上限指标;
5)增加水泥1d、3d水化热上限指标;
6)增加水泥碱含量上限指标;
7)增加对水泥开裂敏感性的限制;
8)增加水泥与减水剂相容性下限指标;
9)增加3d/28d强度比值的上限指标,增加水泥强度28d/365d强度比值的上限指标;
10)增加水泥与减水剂相容性、强度、凝结时间、细度的标准偏差上限指标;
11)水泥初凝时间下限指标变为120min;
12)适当调整目前通用硅酸盐水泥的其他指标。
4结束语
1)半个多世纪以来混凝土耐久性越来越差,水泥质量错误的发展方向是最重要的原因。水泥质量发展方向与混凝土耐久性相悖的主要原因,来自反科学的利益驱动和认识的局限。如不能尽快彻底改变水泥质量的发展方向和现状,混凝土耐久性问题就无法从根本上改观,我国每年数千亿的混凝土建筑物,几十年之后面临的维修和重建费用,数目之大让人不寒而栗。美国目前每年混凝土建筑物的维修费用高达数千亿美元。
2)混凝土耐久性不断劣化的事实,让我们不得不对水泥质量发展方向产生怀疑,欲扭转水泥质量发展方向,则必须从根本上转变水泥质量的唯强度论、唯化学论等一系列错误观念,从根本上修订现有通用硅酸盐水泥标准的框架。
3)将水泥质量作为一个重要的变量,突破现有通用硅酸盐水泥质量标准,研究水泥质量与混凝土耐久性关系。在此基础上重新建立通用硅酸盐水泥质量标准体系。
4)几十年来我国水泥标准一直不断追随西方发达国家,今天,当他们已经走向错误方向的时候,我们应该有勇气走自己的路。