集团动态 News Information
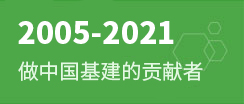
这6种使用减水剂会出现的现象,你都了解吗?
减水剂大多属于阴离子表面活性剂,目前市场上常用的有聚羧酸系减水剂、萘系减水剂等,在维持混凝土坍落度不变条件下,能大幅减少拌和用水量,提高混凝土强度,降低裂缝产生,在混凝土性能调节方面起到重要作用。
然而,因原材料质量下降、工作人员专业度不够等多重因素的影响,掺减水剂的混凝土拌和物会出现多种象,以下进行一一分析解决。
粘罐现象,顾名思义,是指水泥砂浆部分粘在搅拌机筒壁上,导致出机的混凝土不均匀、灰少且整体发粘的现象。这种情况不仅影响了混凝土的质量,还可能增加搅拌机的维护成本,降低生产效率。
缓凝减水剂的作用机制:缓凝减水剂能够显著降低混凝土的水灰比,提高混凝土的流动性,但同时也会改变混凝土的物理和化学性质。在某些情况下,这些变化可能导致混凝土在搅拌机内部分泌出粘性物质,从而附着在筒壁上。
搅拌机类型与轴径比:轴径比接近的滚筒式搅拌机由于搅拌效率相对较低,混合物在筒内的停留时间较长,更容易出现粘罐现象。而强制式搅拌机由于搅拌力度大、效率高,能在一定程度上减少粘罐的发生。
混凝土配比与搅拌工艺:不合理的混凝土配比和搅拌工艺也是导致粘罐现象的重要因素。例如,如果先加入水泥和减水剂再与集料混合,可能会因为减水剂过早与水泥反应而生成粘性物质。
针对使用缓凝减水剂时出现的粘罐现象,可以采取以下策略进行应对:
及时清洗搅拌机:每次搅拌结束后,应及时清洗搅拌机筒壁和搅拌叶片上的残留混凝土,防止其硬化并增加后续搅拌的阻力。
优化搅拌工艺:改变搅拌顺序,先加入集料和部分水进行预拌,使集料充分湿润并分散开来,再逐步加入水泥、余水和减水剂进行拌和。这种方法可以减少减水剂与水泥直接接触的时间,从而降低粘性物质的生成。
选用合适的搅拌机:考虑更换轴径比更大的滚筒式搅拌机或采用强制式搅拌机。这些类型的搅拌机具有更高的搅拌效率和更强的混合能力,能够更有效地避免粘罐现象的发生。
调整混凝土配比:通过调整混凝土中的水泥、水、集料和外加剂的配比,改善混凝土的流动性和工作性能,减少粘性物质的生成。
加强质量控制:在混凝土生产过程中加强质量控制,定期检查搅拌机的运行状态和混凝土的质量指标,确保生产过程的稳定性和可控性。
假凝,是指混凝土在搅拌过程中,由于某种原因使得混凝土迅速失去流动性,表面看似已经凝结,但实际上内部并未完全硬化的现象。这种现象通常伴随着混凝土粘度的急剧增加,导致搅拌困难,甚至发生粘罐现象,严重影响混凝土的生产质量和效率。
水泥化学成分影响:当水泥中硫酸钙(石膏)含量不足时,铝酸钙的水化反应会加速进行,导致混凝土在短时间内迅速失去流动性,形成假凝。这是因为硫酸钙能够调节铝酸钙的水化速度,防止其过快水化。
减水剂适应性差:不同品牌、类型的水泥对减水剂的适应性存在差异。如果所选用的减水剂与当前使用的水泥不匹配,就可能导致减水剂无法有效发挥作用,甚至引发假凝现象。
外加剂掺量不当:在某些情况下,如三乙醇胺等外加剂的掺量超过一定范围(如0.05%-0.1%),也可能导致混凝土迅速初凝但不终凝,形成假凝状态。
针对使用减水剂时出现的假凝现象,可以采取以下策略进行应对:
更换水泥品种:如果当前使用的水泥品种容易引发假凝现象,可以考虑更换其他品牌或类型的水泥,选择硫酸钙含量适中、与减水剂适应性好的水泥品种。
调整外加剂配方:通过适当调整外加剂的配方,如更换减水剂种类、调整减水剂掺量或进行复配等,以改善外加剂与水泥的适应性,减少假凝现象的发生。
补充硫酸钠成分:在外加剂中适量补充硫酸钠(Na2SO4)成分,可以有效调节水泥中铝酸钙的水化速度,防止其过快水化导致的假凝现象。同时,硫酸钠还能增强混凝土的强度和耐久性。
加强搅拌管理:在搅拌过程中加强监控和管理,确保搅拌时间、搅拌速度等参数符合规范要求。同时,定期对搅拌机进行清洗和维护保养工作,防止残留物对后续搅拌造成影响。
优化混凝土配比:通过优化混凝土的配比设计,合理调整水灰比、水泥用量等参数,以改善混凝土的工作性能和流动性。这有助于减少假凝现象的发生并提高混凝土的质量。
不凝现象指的是在掺入减水剂后,混凝土在长时间内(甚至一昼夜)仍未达到预期的凝固状态,或者表面出现泌浆并呈现黄褐色的现象。这种情况不仅严重影响了混凝土的施工进度和质量,还可能对后续工程造成安全隐患。
减水剂掺量过大:减水剂的主要作用是通过吸附在水泥颗粒表面,形成一层润滑膜,从而降低水泥颗粒间的摩擦力,提高混凝土的流动性。然而,当减水剂掺量过大时,过多的润滑膜会阻碍水泥颗粒之间的正常水化反应,导致混凝土无法正常凝固。
缓凝剂使用过量:在某些情况下,为了延长混凝土的初凝和终凝时间,会加入缓凝剂。但如果缓凝剂的使用量控制不当,过量使用也会导致混凝土长时间不凝固。
针对不凝现象,可以采取以下解决方案:
控制减水剂掺量:首先,应严格按照产品说明书和工程要求控制减水剂的掺量。一般来说,减水剂的掺量不应超过推荐用量的2-3倍。虽然在此范围内强度可能会稍有降低,但28天强度和长期强度降低较少,对整体工程质量影响可控。
调整养护条件:在混凝土终凝后,适当提高养护温度并加强浇水养护。这有助于加速水泥的水化反应,促进混凝土的硬化和强度发展。同时,良好的养护条件还能减少混凝土表面的泌水和干裂现象。
重新浇筑:如果混凝土已经成型但长时间未凝固,且无法通过调整养护条件来改善情况,那么可能需要将已成型部分清除掉并重新浇筑。这虽然会增加工程成本和工期,但为了确保工程质量和安全,有时是必要的措施。
加强施工管理:在混凝土施工过程中,应加强施工管理,确保减水剂和缓凝剂等外加剂的准确计量和均匀混合。同时,还应对混凝土的性能进行实时监测和调整,以预防不凝现象的发生。
混凝土强度低是指混凝土的抗压强度、抗拉强度等力学性能指标低于设计要求或同龄期试配结果。这种现象可能表现为混凝土虽已凝结但强度极低,无法满足工程使用要求。强度低不仅会降低混凝土的耐久性和承载能力,还可能影响结构的整体稳定性和安全性。
引气性减水剂掺量过大:引气性减水剂在混凝土中能够引入微小气泡,改善混凝土的抗冻融性和工作性能。然而,当掺量过大时,会导致混凝土内含气量过高,从而降低混凝土的密实度和强度。
振捣不足:在使用引气性减水剂后,如果振捣不够充分,混凝土中的气泡无法有效排出,形成大量微孔,这些微孔会削弱混凝土的强度。
水灰比控制不当:减水剂的主要作用之一是减少用水量,但如果在使用减水剂时未相应减少用水量或反而加大了水灰比,会导致混凝土内部孔隙率增加,从而降低强度。
减水剂质量不合格:减水剂的有效成分含量过低或含有杂质,会直接影响其减水效果和混凝土的性能,导致强度降低。
重新评估与加固:对于已浇筑且强度明显偏低的混凝土部位,应首先进行强度评估。若强度无法满足设计要求,需采取其他加固措施,如增设钢筋网、粘贴碳纤维布等,以提高结构承载力。在极端情况下,可能需要拆除并重新浇筑。
加强振捣:在使用引气性减水剂时,应确保振捣充分,以排出混凝土中的气泡,提高密实度。可采用高频振动器或延长振捣时间等方法来加强振捣效果。
严格控制水灰比:在使用减水剂时,应根据产品说明书和工程要求严格控制水灰比。通过精确计量用水量和减水剂掺量,确保混凝土达到最佳的水化反应条件,从而提高强度。
鉴定减水剂质量:对于怀疑存在质量问题的减水剂批次,应及时进行质量鉴定。通过检测减水剂的有效成分含量、杂质含量等指标,评估其是否满足使用要求。对于不合格的减水剂,应立即停止使用并更换合格产品。
混凝土在掺入减水剂后,本应获得更好的流动性和工作性能,但实际操作中却常常遇到坍落度迅速下降的问题。具体表现为:混凝土出罐后,每延长2~3分钟,坍落度就会减少1~50mm,且伴有明显的沉底现象。这不仅增加了施工难度,还可能导致混凝土性能不稳定,影响最终工程质量。
减水剂适应性差:减水剂与水泥的适应性是影响混凝土坍落度稳定性的关键因素。当减水剂对所使用的水泥适应性差时,无法有效发挥其减水作用,反而可能导致混凝土性能恶化,表现为坍落度损失过快。
气泡外溢与水分蒸发:引气性减水剂在混凝土中能够引入微小气泡,改善混凝土的工作性能。然而,这些气泡在搅拌和运输过程中可能不断外溢,同时伴随着水分的蒸发,导致混凝土体积收缩、坍落度下降。
环境温度与搅拌温度:高温环境会加速混凝土中水分的蒸发和化学反应速率,从而加剧坍落度损失。此外,搅拌过程中的高温也可能对减水剂的稳定性产生不利影响。
混凝土坍落度大:大坍落度混凝土本身具有更高的流动性,但同时也更容易受到外界因素(如温度、湿度、时间等)的影响,导致坍落度损失过快。
查找原因并针对性采取措施:首先应对减水剂、水泥、骨料等原材料进行全面检测,找出导致坍落度损失过快的具体原因。然后针对这些原因采取相应的措施,如更换适应性更好的减水剂、调整水泥品种或掺量、优化骨料级配等。
采用后掺法:后掺法是一种有效的控制坍落度损失的方法。具体做法是在混凝土搅拌1-3分钟后或浇筑前再掺入减水剂,并重新搅拌。这样可以使减水剂更充分地与水泥颗粒接触并发挥作用,减少坍落度损失。
注意加水量的控制:在解决坍落度损失过快问题时,必须严格控制加水量。单独加水虽然可以暂时提高混凝土的流动性,但会破坏混凝土的水灰比平衡,导致强度下降和其他性能问题。因此,在调整混凝土坍落度时,应优先考虑通过调整减水剂掺量或采用其他措施来实现。
在混凝土施工过程中,沉降缝是一个常见但需要注意的问题。这种裂缝通常出现在混凝土浇筑后初凝前后的阶段,表现为短、直、宽而浅的形态,主要集中在钢筋上方区域。沉降缝的出现不仅影响了混凝土表面的美观性,还可能对结构的整体性和耐久性造成潜在威胁。
沉降缝的产生主要与混凝土的粘稠度和沉降性能有关。当混凝土中掺入减水剂后,其流动性得到改善,但同时也可能使得混凝土变得更为粘稠,不易泌水。在混凝土浇筑过程中,如果振捣不充分或浇筑速度过快,混凝土中的骨料和水泥浆体可能无法完全均匀沉降,从而在钢筋上方等区域形成沉降缝。
混凝土粘稠度高:减水剂的加入提高了混凝土的粘稠度,使得混凝土内部的水分和气泡难以排出,影响了混凝土的沉降性能。
振捣不充分:振捣是混凝土施工中至关重要的环节,它有助于混凝土内部的气泡和多余水分的排出,以及骨料和水泥浆体的均匀分布。如果振捣不充分,混凝土中的沉降不均匀现象就会加剧。
浇筑速度过快:过快的浇筑速度可能导致混凝土在尚未充分沉降的情况下就被新的混凝土层覆盖,从而增加了沉降缝产生的风险。
针对沉降缝现象,可以采取以下措施进行预防和处理:
优化混凝土配合比:通过调整混凝土中减水剂的掺量和其他外加剂的种类及用量,降低混凝土的粘稠度,提高其沉降性能。
加强振捣作业:在混凝土浇筑过程中,应确保振捣充分、均匀。特别是钢筋密集区域和混凝土厚度较大的部位,应适当延长振捣时间,确保混凝土内部的气泡和多余水分得到有效排出。
控制浇筑速度:合理安排浇筑顺序和速度,避免过快或过慢的浇筑速度对混凝土沉降性能造成不利影响。
及时处理沉降缝:对于已经出现的沉降缝,可以在混凝土初凝前后及时进行抹压处理。通过抹压可以封闭裂缝,防止裂缝进一步扩展,并改善混凝土表面的平整度。需要注意的是,抹压操作应迅速且均匀,避免对混凝土内部造成过大的扰动。