集团动态 News Information
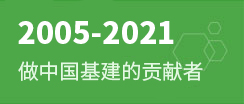
混凝土产生假凝现象的原因分析
摘要:假凝是水泥的一种不正常的早期固化或过早变硬现象。假凝与快凝不同,前者放热量甚微,且经剧烈搅拌后浆体可恢复塑性,并达到正常凝结,对强度无不利影响。碱含量对水泥与减水剂的适应性产生影响,随着碱含量增大,减水剂的塑化效果变差。
假凝是指水泥的一种不正常的早期固化或过早变硬现象。假凝放热量甚微,经剧烈搅拌后浆体可恢复塑性,并达到正常凝结,对强度无不利影响。
假凝现象与很多因素有关,一般认为主要是由于水泥粉磨时磨内温度较高,使二水石膏脱水成半水石膏的缘故。当水泥拌水后,半水石膏迅速水化为二水石膏,形成针状结晶网状结构,从而引起浆体固化。另外,某些含碱较高的水泥,硫酸钾与二水石膏生成钾石膏迅速长大,也会造成假凝。
假凝处理方法:
1、选用适合的水泥。
2、加入适量的添加剂,如减水剂或者缓凝剂。
3、进行剧烈搅拌。
假凝是指水泥的一种不正常的早期固化或过早变硬现象。在水泥用水拌和的几分钟内,物料就显示凝结。假凝和快凝是不同的,前者放热量极微,而且经剧烈搅拌后,浆体又可恢复塑性,并达到正常凝结,对强度并无不利影响;而快凝或闪凝往往是由于缓凝剂不够所引起的,浆体已具有一定强度,重拌并不能使其再具有塑性。
假凝浆体在重拌后,维卡仪试针插入深度的变化即能与正常凝结大致相近,而快凝的水泥却几乎不变。因此,假凝的影响比快凝较为轻微,但仍会给施工带来一定困难。
假凝现象与很多因素有关,除熟料中C3A含量偏高、石膏掺量较多等条件外,一般认为,主要还由于水泥在粉磨时受到高温,使较多的二水石膏脱水成半水石膏的缘故。当水泥加水后,半水石膏迅速溶于水,部分又重新水化为二水石膏析出,形成针状结晶网状构造,从而引起浆体固化。对于某些含碱较高的水泥,所含的硫酸钾会依下式反应:K2S04+CaS04·2H20=K2S04·CaS04·H2O十H20
所生成的假石膏结晶迅速长大,也会是造成假凝的原因。另外,即使在浆体内并不形成二水石膏等晶体所连生的网状构造,有时也会产生不正常凝结现象。有的研究者认为,水泥颗粒各相的表面上,由于某些原因而带有相反的电荷,这种按其本质是触变性的假凝,则是这些表面间相互作用的结果。
实践表明,假凝现象在掺有混合材料的水泥中很少产生。实际生产时,为了防止所掺的二水石膏脱水,在水泥粉磨时常采用必要的降温措施。还应尽量采用无水硫酸钙含量较高的石膏,将水泥适当存放一段时间,或者在制备混凝土时延长搅拌时间等,也可以消除假凝现象的产生。
随着现代化建设的发展,商品混凝土的应用日益普遍。而作为商品混凝土组分之一的减水剂所起的作用及其对混凝土科学技术发展的贡献,已得到了公认。然而,就减水剂应用技术而言,尚有些问题未得到圆满解决。
本文仅从水泥、掺和料与减水剂之间的相互适应性略作浅谈,供同行及工程界相关人员参考。
3.1、 水泥与减水剂的适应性。
水泥的早期水化
当水与高吸湿性水泥粒子接触时,由于水泥中的Na+,K+,Ga2+,SO42-、OH-进入溶液, 表面水解很快形成一薄层无定形的胶体产物。在最初溶解之后,液相中的均匀成核过程或固液界面的非均匀成核过程生成水化物。随后,水化产物的生长受到溶液浓度、反应用水和离子的可得量、反应过程的活化能以及晶体生长的定向要求所控制,在第一阶段后期,水泥粒子完全被一层水化产物所覆盖,阻碍反应物在反应界面向内外扩散,极大地降低反应速度,这一阶段从与水接触开始持续约15分钟。第二阶段叫诱导期,时间从15分钟到4小时。在第二阶段早期,主要是铝酸盐的反应,这时期SO42-的浓度起主导作用。如:
1、SO42-的浓度太低, 过度的成核作用和C-A-H的生长会产生闪凝。
2、SO42-的浓度太高,大量的成核作用和石膏晶体的生长会产生假凝。
3、SO42-浓度合适时,发生几种物理化学反应,钙钒石晶体生成,从C-S-H胶体增加,溶液中的SO42-和OH-浓度增加,水化向水泥粒子内部扩展产生渗透压和机械力。
上述过程确定水泥浆的流变性能和凝结性能,外加剂和水泥反应物的相互作用或外加剂对水泥的扩散过程、成核过程和生长过程的干扰将影响混凝土的性能。水泥的各成分和水的活性依次为C3A>C3S>C2S>C4AF,铝酸盐相和它的水化产物在水化早期起着重要作用。由于铝酸三钙参加硫酸钙的反应生成钙矾石和单硫铝酸钙控制铝酸盐的反应速度,掺加外加剂对硫酸盐控制水化速度的影响必然会影响水泥的水化过程。水泥浆溶液中的硫酸钙必须充分溶解并有足够硫酸盐离子和钙离子供给生成硫铝酸钙。铝酸盐和水直接反应产生闪凝。
假凝可以通过进一步拌和,破坏生成物结构,恢复流动性。闪凝则不同,如果不加水它不可能通过进一步拌和消除它的结构,熟料太热时与石膏共同磨细会使石膏脱水产生半水石膏和无水石膏,半水石膏和无水石膏水化生成石膏会使水泥产生假凝。
3.2、碱含量
现行国家标准GB8076-1997《混凝土外加剂》规定各类混凝土外加剂总碱量(Na2O+0.658K2O)应在生产厂控制值的相对量的5%之内, 对工程应用无指导意义。GBJ119《混凝土外加剂应用技术规范》规定。处于与水接触或潮湿环境中的混凝土,当使用碱活性骨料时,由外加剂带入的碱含量(以当量氧化钠)不宜超过1kg/m3,混凝土总碱量尚应符合有关标准的规定。
碱含量对水泥与减水剂的适应性产生影响,随着碱含量增大,减水剂的塑化效果变差,见下表:
水泥碱含量对减水剂净浆流动度的影响
水泥的矿物组分中,C3A和C3S对水泥水化速度和强度起决定作用。减水剂加入到水泥+水系统后,首先被C3A吸附。在减水剂掺量不变的条件下,C3A含量高的水泥,由于被C3A吸附量大,必然使得用于分散C3S和C2S等其他组分的量显著减少。因此,C3A含量高的水泥减水效果差。
3.3混凝土掺合料与减水剂
3.3.1掺合料的酸碱性
用于混凝土的掺合料种类繁多,为了便于掌握掺合料对混凝土性能的影响,并对其进行更充分、合理的利用,将其按化学成分作进一步的分类, 将掺合料按其化学成分当中Si 2 O含量的高低划分为酸性、中性和碱性三类。其中,酸性掺合料的Si2O含量为>65%, 中性掺合料的52~65%,碱性掺合料的<52%。当然,这是一种粗略的划分, 酸性氧化物还有Fe3O4,Al2O3等,但因他们在掺合料中的含量较低。酸性较弱而不作讨论。 掺合料的Si2O含量亦即其酸碱性不仅影响到水泥混凝土的各龄期强度,而且直接影响到混凝土减水剂的作用效果及混凝土的和易性等,这可从以下两方面进行分析:
第一方面,掺合料的酸碱性与其表面的亲水性和憎水性密切相关。酸性愈强的材料,表面的亲水性愈大,碱性愈强的材料,则憎水性愈大。亲水性材料的表面易被水润湿,且水能通过毛细管作用而吸入材料内部,憎水材料则能阻止水分渗入毛细管中,从而降低材料的吸水性。所以,配制混凝土用的掺合料酸性愈强,吸附水分的能力也随之增强。在混凝土中掺和水用量相同的条件下,对混凝土流动性的影响也更加不利。如果要保证混凝土具有良好的施工和易性和强度,就必须相应提高减水剂的效能或增加其掺量。
第二方面, 掺合料的酸碱性即亲水性或憎水性,也直接影响到它与减水剂的吸附效果,从而影响到减水剂的使用效果。若商品混凝土的掺和料本身亲水性很强,即酸性很强,除了对水有很强的吸附能力之外,对减水剂分子的亲水端也同样具有吸附能力,从而削弱减水剂憎水基团在固体表面的定向吸附作用,在一定程度上扰乱了减水剂分子在固体表面吸附的规则排列,在这种情况下, 要保证减水剂的分散效果和混凝土的流动性,就必须加大减水剂用量,在固体颗粒表面形成多分子吸附层,以平衡电性不同的带电粒子, 相反,如果掺合料的憎水性强,即碱性强,则可相应减少减水剂的用量,同样能保证混凝土的流动性要求。
3.3.2掺合料的活性
水泥和混凝土掺合料的活性对混凝土28天强度的影响是众所周知的。然而,对混凝土和易性的影响以及与减水剂的适应性常被人们所忽视。活性高的掺合料固然对提高混凝土28天强度有利, 但对混凝土的流动性及其与减水剂的适应性却有不利的影响。一般来讲,掺合料的活性越高,其表面能也越大,对减水剂的化学吸附和物理吸附能力更强,因而在固体颗粒表面的每一个吸附活性中心点都会吸附更多的减水剂分子,那么在比表面积相同的情况下, 要使减水剂完全布满颗粒的表面,就需要吸附更多数量的减水剂,才能保证它对颗粒之间的分散效果,使混凝土的流动性不致降低
3.3.3 掺合料的细度
在掺合料种类和用量以及混凝土流动性要求相同的情况下,掺合料的粉磨细度细,比表面积大,拌制混凝土时所需要的水分和减水剂用量无疑要多,也就是说掺合料的细度愈细,与减水剂的适应性愈差。同时,掺和料的颗粒级配和表面形态对其与外加剂适应性的影响也相当重要, 良好的颗粒级配和较光滑的颗粒表面,对降低混凝土的孔隙率,提高减水剂的作用效果是非常有利的。对商品混凝土来说,过多的减水剂用量,不仅仅是增加费用的问题,掺过多的减水剂会增大混凝土的干缩现象,容易产生干缩裂缝;并对混凝土的硬化速度产生影响。
水泥和混凝土掺和料的组分特性,是影响混凝土减水剂适应性好坏的重要因素。因此,在配制商品混凝土时合理选择水泥及掺和料的种类,调整适当的搭配比例,并适当控制减水剂掺量比例,即可改善水泥和混凝土掺和料与混凝土减水剂的适应性,从而使商品混凝土的和易性、耐久性及强度得到均衡有效的提高。