集团动态 News Information
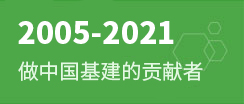
堵管,又堵管,泵送混凝土为什么总堵管呀……
混凝土拌合物的初始状态是衡量配合比好坏最直观的方法,在混凝土配合比试拌的过程中,往往会遇到一些工作性不能满足要求的情况。引起这些现象的原因多种多样,有混凝土配合比设计方面的,有原材料质量方面的,也有外加剂与混凝土原材料相容性方面的。要找到问题的原因所在,才能有效调整混凝土的工作性,以下几点是根据一些混凝土拌合物常见的状态而采取的一些方法,希望有所帮助,同时也需要实践中多多总结。
混凝土拌合物包裹性良好,保水性和粘聚性良好,坍落度偏小。混凝土坍落度偏小,可以分为两种:一种是设计坍落度偏小,另一种是坍落度损失过快造成的坍落度偏小。针对第一种现象,一般采用保持水胶比不变,适当增加浆体用量,必要时提高外加剂用量即可满足要求。
混凝土拌合物损失过快,通常表现为,一是5min内损失很大,即假凝或者速凝。二是混凝土拌合物20min左右损失严重,主要是水泥中C3A含量高或者硬石膏含量高,或者外加剂中的还原糖与石膏反应造成的。三是混凝土拌合物1h内一直有损失,主要是C3A含量高或者温度高的新鲜水泥。
(1)水泥与外加剂相容性差,甚至外加剂中的某些成分与水泥中石膏发生影响。
(2)混凝土的矿物掺合料需水量大,吸附较多的外加剂,如需水量较大的粉煤灰、煤矸石等。
(3)水泥中的可溶性碱与可溶性硫酸盐与C3A比例不协调。
(4)外加剂中母液含量不足,减水与保坍组分比例不当,或者缓凝组分用量不足,尤其水泥温度高或气温高时未增加用量。
(5)混凝土骨料吸水率偏大,如风化砂,或砂含泥量过大。
(6)配合比设计时,用水量不足,尤其是使用聚羧酸减水剂时对用水量敏感。
针对以上原因,可以采取以下措施:
(1)适当提高外加剂用量。
(2)调整外加剂配方,改善可溶性碱与可溶性硫酸盐与C3A比例,针对水泥选用合适的缓凝组分。
(3)降低或者更换需水量较大的矿物掺合料,降低对外加剂的吸附。
(4)降低或者更换含泥量、需水量较大的细骨料用量,减少对拌合水及外加剂的吸附。
混凝土拌合物坍落度满足要求,但拌合物的粘聚性差,保水性差,混凝土发散,浆体对部分粗骨料不能包裹,使其“浮”在拌合物表面。也常常伴有泌水、泌浆现象,但不抓底,缺陷严重时也有离析现象。造成这一现象可能有以下原因:
(1)混凝土拌合物设计坍落度与浆体量不匹配,配合比胶凝材料用量小,浆体量不足,如浆体量低于280L/m3,而设计坍落度大于200mm,甚至更大,浆体填充后不足以包裹骨料。
(2)混凝土拌合物中浆体偏少,砂率过大,细骨料含量大,骨料比表面积增加,浆体不足以有效黏结骨料,粘聚性差,混凝土发散。
(3)砂石骨料粒径单一,空隙率偏大,粗骨料中5~10mm颗粒含量偏少,空隙率偏大,细骨料细度模数偏大,粒径大于0.6mm颗粒含量大,0.315mm颗粒含量较低,不足15%。
(4)粗骨料中5~10mm颗粒含量偏多,其空隙率较大,细骨料细颗粒含量不足,盲目增加砂率,造成混凝土拌合物中2.36mm~10mm颗粒严重超标,浆体不足以包裹,造成混凝土拌合物发散。
针对以上原因,可以采取如下措施:
(1)调整配合比,保持水胶比不变,增加浆体用量,提高混凝土拌合物的黏聚性,包裹性。
(2)调整粗骨料级配,降低空隙率,增加细砂用量,改善保水性。
(3)根据实际情况,适当调整砂率,浆体粗骨料用量,改善混凝土包裹性。
(4)在外加剂中复配引气组分。
混凝土拌合物坍落度、保水性均可以满足要求,就是混凝土拌合物看起了像用水拌合的,动感不足,常常扩展度小。造成这一现象主要有以下原因:
(1)外加剂用量偏低造成混凝土拌合物流动性不足,扩展度差。
(2)骨料级配差,某一粒径颗粒缺失,骨料粒形差造成混凝土流动性不足;
(3)细骨料中0.315mm以下颗粒含量偏多,或者骨料含泥量偏多,造成混凝土拌合物黏稠。
(4)胶凝材料用量偏高,混凝土拌合物黏稠。
针对性措施:
(1)适量增加外加剂用量,提高混凝土流动性,必要时可以在增加外加剂的同时,降低用水量。
(2)采用骨料复配技术,改善骨料级配,提高混凝土拌合物的工作性。
(4)高强度等级混凝土可以采用降黏型外加剂,降低拌合物浆体黏度。
混凝土拌合物同时出现以上三种不良状态,即混凝土拌合物坍落度小,扩展度不足,同时保水性、包裹性差,甚至粗骨料不裹浆,有离析现象。这一现象的原因要比以上复杂,既具有以上三种各自的单项原因,也有综合原因。具体可以从以下方面着手解决:
(1)混凝土浆体偏少,粗骨料级配差,空隙率大,粗骨料偏粗或者偏细,级配不良,某一个或者几个级配含量不足。
(2)原材料质量差,需水量或者吸水率大,或者外加剂与原材料相容性差。
(3)水泥中可溶性硫酸盐或可溶性碱含量严重不足。
对策主要有:
(1)进行细骨料复配,改善粒径小于0.315mm颗粒含量,控制其18%左右。
(2)粗骨料复配使用,改善骨料级配,降低空隙率。
(3)适量调整砂率,改善混凝土的粘聚性、保水性。
(4)保持水胶比不变,调整浆体用量。
混凝土拌合物搅拌完成后,拌合物表面气泡较多,有时不断破裂。混凝土浇筑硬化后,侧面气泡比较多,严重时表层出现泡沫状的砂浆层。导致混凝土拌合物气泡较多的原因有:
(1)砂细度模数偏大,缺少细颗粒,同时配合比砂率较小。
(2)使用含有氨化物残留的粉煤灰,在碱性环境下分解放出氨气。
(3)聚羧酸减水剂合成时,使用甲基、二甲基结构成分量大,或者双氧水用量大,或复配引气剂用量、品种不合理,造成外加剂含气量高。
(4)混凝土配合比设计时,外加剂用量偏大,常常出现表层一层气泡,并不断溢出。
针对上述原因,可采取以下措施:
(1)对细度模数偏大的细骨料,适当复配细砂,或者提高胶凝材料用量,并根据需要调整砂率。
(2)减少含氨残留粉煤灰用量,并适当延长搅拌时间。
(3)对聚羧酸减水剂实行“先消,后引”,降低大气泡含量,合理增加小气泡数量。
(4)适量降低外加剂用量,降低混凝土泌浆现象,克服气泡溢出。(文章来源:砼话)