集团动态 News Information
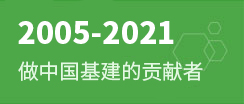
“瘦身水泥”是现代混凝土质量问题的症结所在
现代混凝土是以高流动性、低水胶比、掺加外加剂和大量矿物掺合料为主要特征,以高性能为代表的混凝土。
自上世纪九十年应用以来,由于其大大降低劳动强度,加快施工进度,且节能环保,加之其具有“高性能”的华丽外衣而深受建设者的喜爱,为此,人们对其倾注了极大的工作热情并寄予厚望。
可是,当残酷的质量现状特别是质量事故摆在人们眼前的时候,人们往往唯恐躲之不及,但又欲罢不能而从蹈覆辙,这不得不让人重新思考现代混凝土质量问题的症结到底在哪、方向何在。
经过多年的工程实践和对比分析,笔者认为,导致现代混凝土质量问题突显的内在根源在于瘦身水泥,而瘦身水泥又恰恰是各方人员都不愿意接受的残酷的现实,因为它动摇了人们长久以来引以为豪的现代混凝土应用的政策根基和企业利益,也就是法规权威、节能环保、加快进度和降低成本。
瘦身水泥的具体特征可以从以下两个方面来表述,
一是随着水泥生产技术的不断进步,水泥矿物的平均颗粒粒径越来越小,即水泥的比表面积越来越大。
二是用矿物掺合料替代部分水泥以后,每立方米混凝土中的水泥用量越来越少,而矿物掺合料用量越来越多。
以上水泥粒径小用量少的特征,都是由最初有益的量变,逐渐演化为今天有害的质变,其实质就是混凝土28天以后的强度几乎不增长,密实性不提高,自愈能力削弱,裂缝不断增加,耐久性越来越差,而最终结果是导致混凝土结构质量问题和质量事故不断发生。
下面,笔者通过旁征侧引和对比分析,进一步阐述瘦身水泥在工程中的具体危害,不妥之处,恳请指正。
众所周知,近200年来水泥的发展历史,可以说就是一部如何将水泥磨得更细的历史。水泥生产企业要想使其产品的综合效益达到最大化,就是要想办法让水泥矿物所积蓄的能量在28天内全部释放出来。
最直接最有效的办法就是将水泥矿物磨得更细,而国家标准不设细度上限又为水泥生产企业提供了一个磨细的平台,所以,磨细也就成了必然趋势。
当前,水泥标准是以28天强度作为评定基准的,至于28天后强度如何发展,水泥标准并没有给出明确的规定和要求,以至于水泥生产企业只要按保证28天强度进行水泥生产就可以了。
其实,混凝土28天以后的强度发展除了与水泥中的矿物成分比例及后续的养护条件有关外,还与水泥矿物颗粒粒径的大小有直接的联系。
以硅酸盐水泥中最大含量的硅酸三钙矿物为例,28天的水化深度大约是10um,相对于颗粒粒径绝大多数在30um以下的水泥而言,28天水化已完成90%以上,也就是说,28天后即使养护条件再好,混凝土强度已经没有多少增长的余地。
到目前为止,对混凝土强度长期发展最有说服力的应是日本小樽港持续长达百年的相关试验数据。根据资料介绍,始建于1897年的小樽港,在建设初期制作了6万多个试件,放在海水中、大气中、淡水中分别进行长期耐久性试验,试验结果表明,三者的长期强度发展趋势是基本一致的。
其中,试件在自然的大气环境中存放30~40年强度达到最高,大约提高100%,然后逐年下降,存放95年,强度从最高点下降约40%,但仍高于28天强度20%,也就是说,早期的混凝土寿命在百年以上,而当年所用水泥的颗粒粒径是200um方孔筛筛余量小于10%,其平均粒径远远大于目前国内标准使用的80um方孔筛筛余量小于10%的水泥平均粒径。
为了与小樽港数据进行对比,日本海洋工程研究所也进行了相关试验。试验结果表明,在海洋气候环境条件下,对于比表面积下限在250㎡/kg的水泥,混凝土自然存放5年抗压强度达到最高,增长约40%,然后逐年下降,至10年甚至低于原来的28天强度。
从以上数据对比分析可知,水泥颗粒粒径的大小对混凝土强度的长期发展起着决定性的作用,当水泥颗粒粒径大于30um时,粒径越大,混凝土28天后强度增长的幅度也越大,持续增长的时间也越长,
而目前的国家标准,将水泥比表面积下限定在相对较高的300㎡/kg,可实际生产的水泥比表面积多在360~400㎡/kg之间,相应的水泥颗粒粒径绝大多数都在30um以下,虽然有利于提高混凝土的早期强度,
但是,对于混凝土强度的长期发展却是极为不利的,加之有的水泥生产企业为了追求利润的最大化,会将水泥磨得越来越细,早强特征越来越明显,在此前提下,期盼通过后期强度的大幅增长来保证混凝土的耐久性几乎是不可能。
而恰恰相反的是,混凝土强度的长期发展将会由短期的上升很快转为逐年下降,国内多起钢筋混凝土桥梁、高架桥质量事故大都发生在使用期满十年这一关键的时间节点之后也就不足为奇,
因为以当年的水泥比表面积标准与资料日本海洋工程研究所的水泥比表面积进行对比可以推断,如果在配合比设计时施工企业没有大幅提高混凝土配制强度,实际结构混凝土强度已自然下降至设计值以下,发生质量事故也就在所难免。
由此可见,现有水泥与过去传统水泥的最大差异就是在满足28天强度要求的前提下,将原有传统水泥所隐含的巨大的强度安全储备提前予以透支,而这部分被提前透支的强度储备,正是为了抵御各种有害介质长期侵蚀导致强度不断降低提供保障的,一旦缺失,对部分结构的长期耐久性来说后果不堪设想。
上述结论,也正好回答了过去人们常提起的一个问题,那就是在水泥生产工艺和技术不断进步的今天,为什么会出现过去的水泥比现在的水泥好、国外的水泥比国产的水泥好的根源所在。
另外,强度储备被提前透支对结构所造成的不良后果具有极强的隐蔽性,更有人们难以辩驳的法理支撑,因为水泥毕竟是过程产品,而非实体结构,在这一点上,作为建设者我们必须保持清醒的认识。
鉴于目前国内混凝土强度在自然环境中长期发展的相关数据鲜有见之,更多的是引用实验室标养试件数据而缺乏说服力;
另外,对于我们每个人身边住用的建筑工程来说,由于混凝土表面都进行了装饰装修,使混凝土与外界环境隔绝而对其起到了很好的保护作用,混凝土强度也就不会因有害介质的侵入而大幅降低并发生质量事故,从而也就自觉或不自觉地影响了人们对混凝土强度长期发展的高度重视和研究,故这一直是被我们所忽视的问题而鲜见提及。
杨文科先生在《现代混凝土科学的问题与研究》一书中谈到,水泥是混凝土之母,是混凝土的核心原材料,但是,在商品混凝土快速发展的今天,矿物掺合料的大量使用越来越受到热捧,其地位已经到了与水泥不相上下的地步,是现代混凝土不可或缺的组分之一。
固然矿物掺合料的使用有其科学合理的一面,但也必须清醒地看到,如使用不当还会带来负面影响,甚至会给工程带来灾难性的后果,这一点,必须引起我们的高度重视。
众所周知,火山灰质矿物掺合料本身并无胶凝性能,只有与水泥水化后生成的氢氧化钙进行二次反应,才能生成难溶的水化硅酸钙凝胶,从而提高混凝土的强度和密实性。如果混凝土中没有足够多的水泥来提供氢氧化钙反应物,部分矿物掺合料的二次水化也就成为不可能,问题在于水泥水化能生成多少氢氧化钙,而各种矿物掺合料的火山灰质反应又需要多少氢氧化钙。
对于这一问题,理论上并没有得到很好解决,更没有法规依据可循,从而导致大掺量矿物掺合料的使用问题存在诸多的不确定性,对混凝土质量带来不利影响也就不可避免,
比如说,在施工现场我们常常看到的大面积网状裂缝及楼屋面板常常发生的大面积渗漏现象,这些都与矿物掺合料的二次反应没有达到预期的凝结效果而使其转化为细砂组分有直接的联系,这是其一。
其二,商品混凝土绝大多数都是用普通硅酸盐水泥进行混凝土配置,依据国家水泥标准,普通硅酸盐水泥中的混合材参量必须控制在20%以内,可据国家建材部门前期的调查资料介绍,除部分水泥大型企业外,大多数水泥中小企业混合材参量均超标,最高参量甚至高达47%,
而当前的施工验收规范对此又没有提出强制性检测要求,甚至连部分地方政府的检测机构都不开展此项业务,导致施工企业束手无策,这无形之中,也就为不法企业大开方便之门,这是当前瘦身水泥最隐蔽最核心的症结之一,
而更为严重的是,由此导致对部分混凝土质量问题和质量事故的责任认定,都将可能会带来颠覆性的结果,教训的吸取也就成为空谈。
其三,水泥必须进行安定性检测是国家水泥标准的明确要求,但是,当采用胶凝材料替代水泥以后,胶凝材料的安定性问题已经超出了水泥标准的管辖范畴,而相应的其它规范标准又不涉及安定性检测的内容,导致混凝土体积稳定性问题经常发生也就不足为奇,
特别是随着混凝土中掺合料品种和用量的不断增加,水泥用量越来越少,对混凝土体积稳定性取决定性作用的已不是水泥,而是胶凝材料组合。由此可见,现有的规范标准仅对水泥进行检测是不够的,必须增加胶凝材料组合的安定性检测,只有这样,才能最终确保混凝土具有良好的体积稳定性,这是当前规范标准间的盲区。
其四,混凝土路面必须具有良好的耐磨性这是不言而喻的,但设计规范、施工验收规范对混凝土耐磨性的要求却没有明确的量化控制指标,虽然道路水泥标准对水泥的耐磨性有相关的要求,
但是,在矿物掺合料用量越来越多而水泥用量越来越少的今天,原有基准水泥的耐磨性已被弱化,由此导致路面起灰起砂的问题经常发生也就成为必然,即使对簿公堂,法官也难以依法判定,因为耐磨性要求是隐含的,并非规范或图纸明确的,相关的案例也并不少见,这同样是规范标准间的盲区。
其五,当前矿物掺合料中使用量最大的是矿渣和粉煤灰,众所周知,矿渣和粉煤灰的密度均小于水泥的密度,特别是粉煤灰差距更大,这一差距给施工带来了巨大的困难,
因为在混凝土浇筑和振捣过程中,密度大的水泥会往下沉,而密度小的矿物掺合料会往上浮,呈现微观上的分层离析,从而使构件顶部和表面掺合料含量过大而水泥含量过小,底部则反之。
由此造成的不良后果除构件强度上下不均外,梁顶、柱顶、板顶经常开裂已经成为不争的事实,特别是柱顶,开裂现象相当普遍,且水泥用量越少,掺和料用量越多,开裂问题愈加突出,至今难以解决。
作为当前的建设者,虽然我们无法改变规范标准的现状,但我们完全可以想方设法规避其可能带来的风险,并确保混凝土结构在其使用年限内安全可靠的工作。
一是将水泥比表面积控制在300~350㎡/kg之间,最大限度的保证混凝土28天后强度仍有较大幅度的增长,同时,适当提高混凝土配合比设计时的配制强度,增强混凝土抵御各种有害介质长期侵蚀的能力,确保混凝土结构的长期耐久性。
二是在进行混凝土施工配合比设计之前,必须对水泥中的混合材含量进行检测,确保最终混合材和掺合料总量控制的真实性和有效性,同时,在混凝土施工配合比设计完成后,应对所选用的胶凝材料组合进行安定性检测,以最终确保胶凝材料组合具有良好的体积稳定性。
三是对于混凝土表面有耐磨性要求的路面、码头面层、机场道面等,除按第一点控制比表面积外,应优先选用道路硅酸盐水泥或硅酸盐水泥,不宜使用矿渣水泥、粉煤灰水泥或复合水泥,更不宜在混凝土施工配合比设计时掺加矿渣、粉煤灰等矿物掺合料,以确保混凝土具有较强的表面耐磨性。
四是对于不同环境、不同结构、不同保护层厚度的混凝土,其矿物掺合料的最大参量应严格按《混凝土结构耐久性设计规范》(GB/T50476-2008)的条款执行。
综上所述,现代混凝土的质量通病多是因瘦身水泥而引起,这里,既有规范标准间不协调的因素,也有我们自身监管不到位,措施不得力的原因,记得英国标准界有句名言,大意是“标准的缺陷,不能完全免除使用者的责任。”
也就是说,规范标准告诉我们的是方法和行为准则,至于如何选择与决策,主要取决于我们每个人每个团队的责任与智慧。
客观的讲,无论是瘦身水泥自身还是矿物掺合料的使用,都有其积极的一面,比如说,前者有利于生产高强水泥、早强水泥,后者可以充分利用工业废渣、减少二氧化碳排放、降低建设成本等等,但是,其负面影响对许多结构来说也是绝对不能接受的,甚至会带来灾难性的后果,对于这一点,我们决不能漠视。
所以,作为建设者,我们必须始终坚持从混凝土质量的系统把握与控制出发,针对不同项目、不同结构部位及不同的环境条件,分别采取相应的应对措施,既要瞻前,更要顾后,趋利避害,这样,才能确保我们的建设项目经得起时间的检验和历史的考验,履行好我们建设者应尽的责任与义务,促进社会的科学发展、和谐发展。